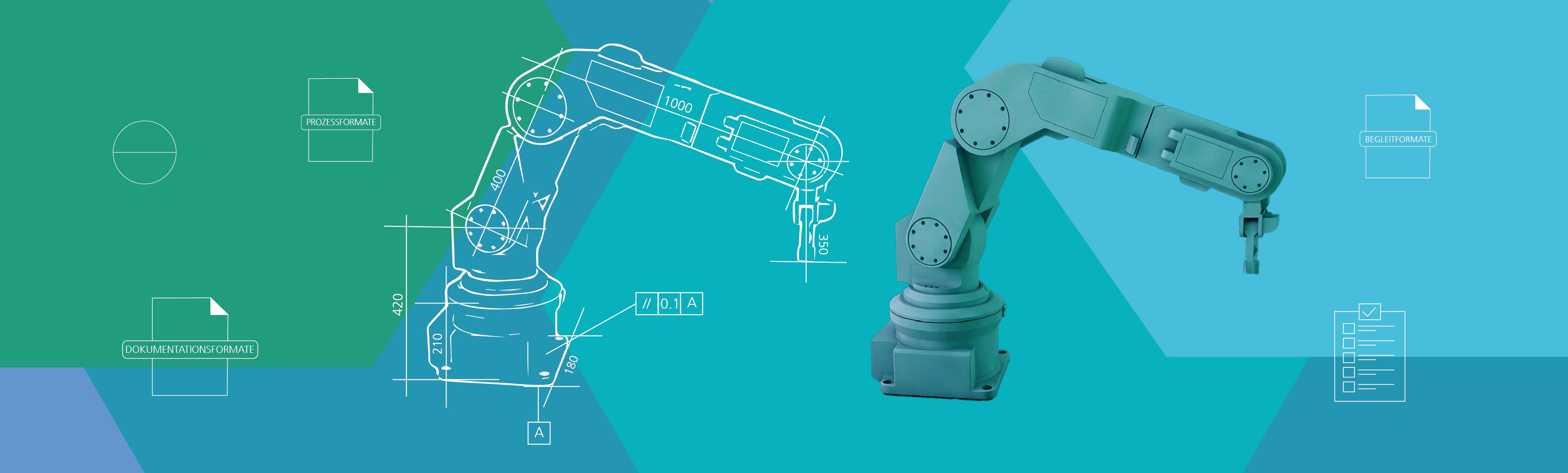
Die heterogene Systemlandschaft über die gesamte Prozesskette hinweg erschwert einen effizienten und effektiven Austausch digitaler Daten und Informationen zwischen Kunden und deren Lieferanten. Kollaboratives Engineering gewinnt mit der Digitalisierung von Produktionsketten für viele Unternehmen eine völlig neue Bedeutung. Über Unternehmens- und Systemgrenzen hinweg muss ein reibungsloser Ablauf gewährleistet werden, der zumeist mit einer effizienten Vermittlung der benötigten digitalen Daten steht und fällt.
Die 3D-Modellierung ermöglicht einen flexiblen Informationsaustausch zwischen Ihrem Unternehmen und den internen wie externen Partnern, da Sie die bisherigen Restriktionen durch verschiedene Softwarelandschaften umgehen können. Durch die erweiterten Möglichkeiten in der Arbeit mit Lieferanten oder für unterschiedliche Kunden erhalten Sie einen entscheidenden Wettbewerbsvorteil und somit einen deutlichen Mehrwert in der gemeinsamen Zusammenarbeit. Auch auf interner Ebene lassen sich Meetings effizienter gestalten und interdisziplinär verwirklichen. Unsere Expertinnen und Experten analysieren Ihre Anforderungen und entwickeln ein auf Ihr Unternehmen maßgeschneidertes, digitales Konzept über die eigenen Unternehmensgrenzen hinweg.
Durch unsere langjährige Erfahrung im Digital Engineering liefern wir Ihnen einen 360°-Blick auf die ganzheitliche Prozessbeschreibung von passenden Use Cases für die digitale Produktion in Ihrem Unternehmen. Unsere Expertinnen und Experten begleiten Sie bei der Definition von Informationsträgern, die in Ihrer digitalen Fabrik eingesetzt werden können und legen für diese die abzubildenden Informationen fest. Gemeinsam identifizieren wir neutrale Datenformate, die Verluste beim system- und organisationsübergreifenden Datenaustausch reduzieren.
Als Institut für angewandte Forschung verfügen wir über Partnerschaften mit einer Vielzahl unterschiedlicher Softwarehersteller und greifen daher auf einen großen Pool an klassifizierten, neutralen Datenformaten zurück, aus dem wir je nach Ihren individuellen Anforderungen eine optimale Auswahl treffen können. Dazu bedienen wir uns auch an etablierten Methoden (z. B. SADT, paarweise Vergleiche und Nutzwertanalysen), um Ihnen ein wissenschaftlich fundiertes Ergebnis zu liefern.
Durch zeichnungslose Produkt- bzw. Maschinenbeschreibung via 3D-Master können Sie Kosten und Ressourcen sparen in der…
- Konstruktion: 5-10 Prozent Einsparung bei der Ersterstellung; 10-30 Prozent Einsparung beim Änderungswesen durch Entfall der CAD-seitigen Zeichnungserstellung
- Freigabe: Reduzierter Aufwand bei der Zeichnungs- bzw. Qualitätsprüfung im Freigabeprozess
- Produktionsplanung und -steuerung:
- Simulation: Direkte Integration und Nutzung des 3D-Masters in Simulationswerkzeugen mit automatischer Verarbeitung der Inhalte
- Zusammenarbeit: Effizienterer und effektiverer Datenaustausch mit externen Partnern mit unterschiedlichen Softwaresystemen, effizientere Meetings insbesondere bei interdisziplinären Teams durch angereichertes 3D-Modell, Erweiterung des Pools an möglichen Lieferanten durch weniger Restriktionen im Bereich der Softwarelandschaft sowie höhere Qualität der digitalen Daten durch reduzierte Verluste beim Datenaustausch
Durch neue Use Cases in der digitalen Produktion, z. B. virtuelle Inbetriebnahme, erreichen Sie eine…
Unser Vorgehen zur Implementierung eines 3D-Masters in Ihrem Unternehmen richtet sich ganz nach Ihren unternehmensspezifischen Bedarfen. So besteht auch die Möglichkeit, einzelne Arbeitsschritte anzupassen oder wegzulassen.
Wir legen in Kleingruppenworkshops gemeinsam fest, welche Daten und Informationen über welche Informationsträger abgebildet werden sollen. Diese Träger bestehen aus einem digitalen Modell der zu untersuchenden Produkte bzw. Produktionssysteme.
Parallel dazu beschreiben und analysieren wir in einem Workshop für Sie relevante Use Cases bezüglich Ihrer internen und externen Kollaborationen unter der Verwendung von etablierten Methoden.
Gemeinsam leiten wir funktionale Anforderungen an die Datenformate Ihrer geplanten digitalen Produktion ab. Hier stellen wir Ihnen auch weitere Zusatzinformationen bereit.
Sie erhalten von uns auf Basis der Use Cases eine konkrete Empfehlung für die Datenformate, die für Ihre Produktion geeignet sind.
Befähigt durch unsere Zusammenarbeit mit einer Vielzahl an Herstellern untersuchen wir gemeinsam die Umsetzungsmöglichkeiten der festgelegten Parameter für eine Beispielbaugruppe Ihrer digitalen Fabrik.
Je nachdem, ob Ihr Unternehmen auf Kunden- oder Lieferantenseite steht, formulieren wir die für Sie spezifischen Anforderungen an die Datenübertragung.
Auf Grundlage Ihrer neuen Engineering-Standards erstellen wir abschließend ein »Big Picture« für Ihren Digitalen Zwilling.
Sollte in Ihrem Unternehmen an dieser Stelle weiterer Bedarf an unserer Zusammenarbeit bestehen, begleiten wir Sie gerne in einem Anschlussprojekt mit der richtigen Expertise für Ihren Digitalen Zwilling (siehe blauer Infokasten).